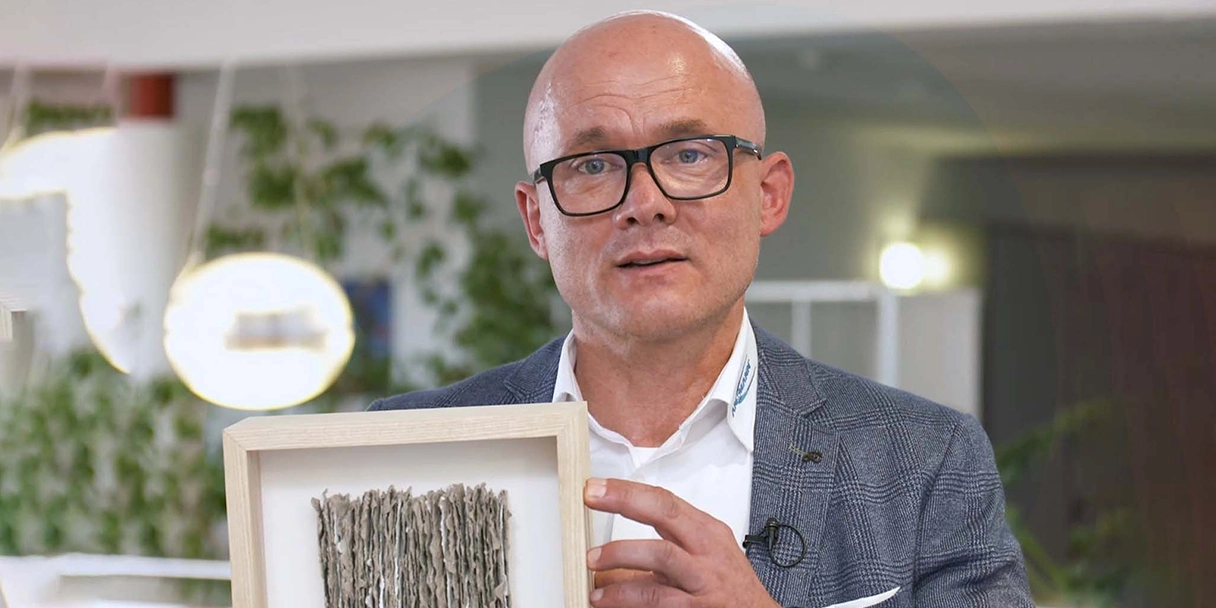
06
.
12
.
2021
ANSMANN wins innovation award with "BioBattery" project
ANSMANN wins innovation award with "BioBattery" project - supported by the Fraunhofer Institute in Darmstadt.
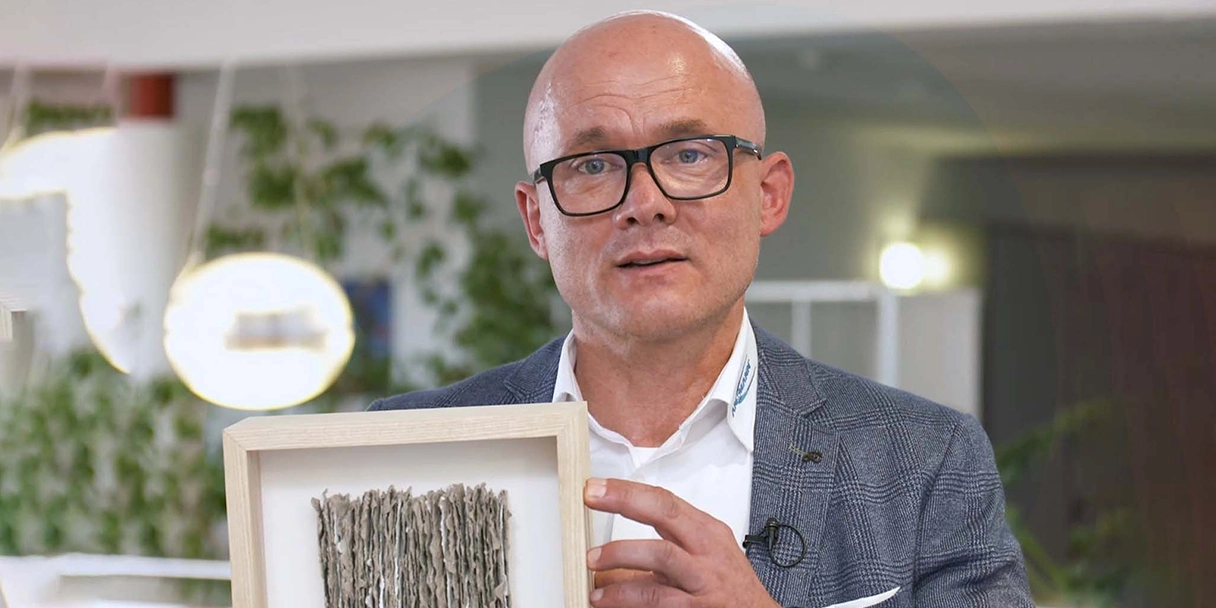
The "BioBattery" project
- supported by the Fraunhofer Institute in Darmstadt - on the use of renewable raw materials, was successfully completed at the end of August 2021.
Already awarded first place in the Future Prize of the Main-Tauber district in the middle of the year, Alfred Bergold and Patrick Megerle from ANSMANN AG were able to receive the Bioeconomy Innovation Prize Baden-Württemberg from Minister Peter Hauk on 18.11.21 in Stuttgart.
The Biobattery project was born from the interaction of three points:
- the need to implement changed specifications of standards.
- the goal of being able to respond individually to customer wishes.
- the desire to also fulfill our socio-political responsibility.
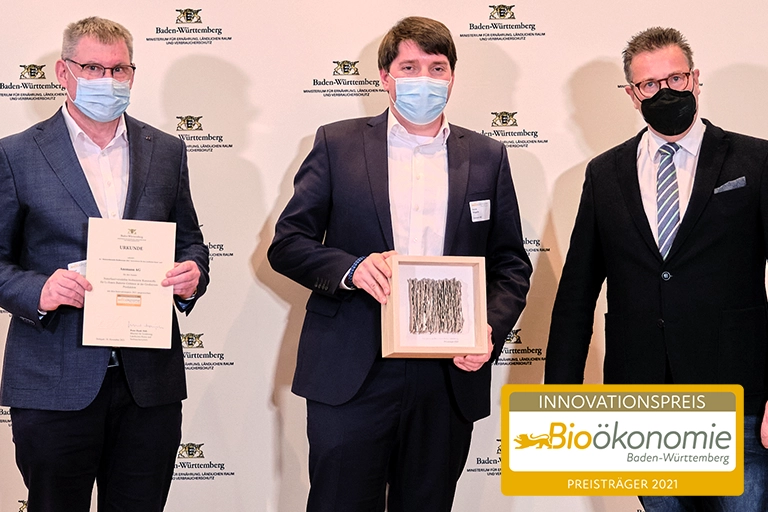
This resulted in a research project in close cooperation with the Fraunhofer Institute for Structural Durability and System Reliability in Darmstadt for the development of natural fiber-reinforced plastics for large-scale lightweight construction using the example of a Li-ion battery housing.
In a first work package, an overview of the possible applications, the standards to be considered, and the resulting required mechanical properties of the plastic components was prepared.
In a second step, suitable natural fibers were then qualified. For a more intensive consideration, hemp, flax, ramie and sisal could be identified.
These natural fibers were compared with respect to the relevant properties of temperature stability, availability of consistent qualities and moisture absorption.
The team chose flax fiber as the fiber with the best temperature stability, which is also available with consistent qualities.
The Fraunhofer Institute was able to further develop an existing machine for melt impregnation so that it could finally process flax fiber fabric.
This is how the sheet material, the so-called organic sheets, came into being. The biggest challenge here was to set the parameters of the machine so that the temperatures and feed rate produced consistent results. Sheets and insert strips were cut from the roll material to achieve the required reinforcements at the corresponding positions of the battery housing. The company Dürr Kunststofftechnik from Schöntal supplemented the existing injection molds and converted them so that the housing parts could be processed on their machine.
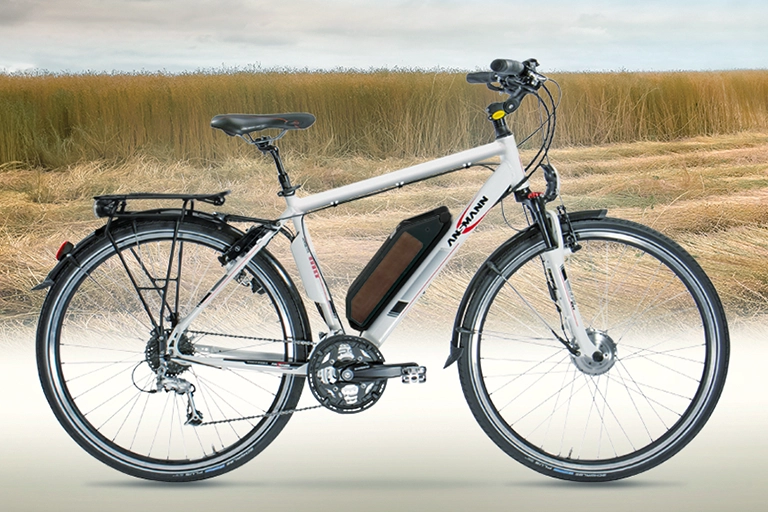
In a joint workshop together with the Fraunhofer Institute at the Dürr company, the appropriate machine setting for the sample production was found. From the manufactured housing parts, Alfred Bergold's team produced finished down tube sample batteries for e-bikes in ANSMANN AG's battery pack production and mounted them on bicycles.
The developed technology can be used for all applications of plastic housings, where hybrid components with natural fiber reinforced sheets improve the mechanical properties of the parts.
In addition, we submitted the BioBattery project to the "100 Companies and More for Resource Efficiency" program, which honors new examples of excellence for improved resource efficiency in production.